About
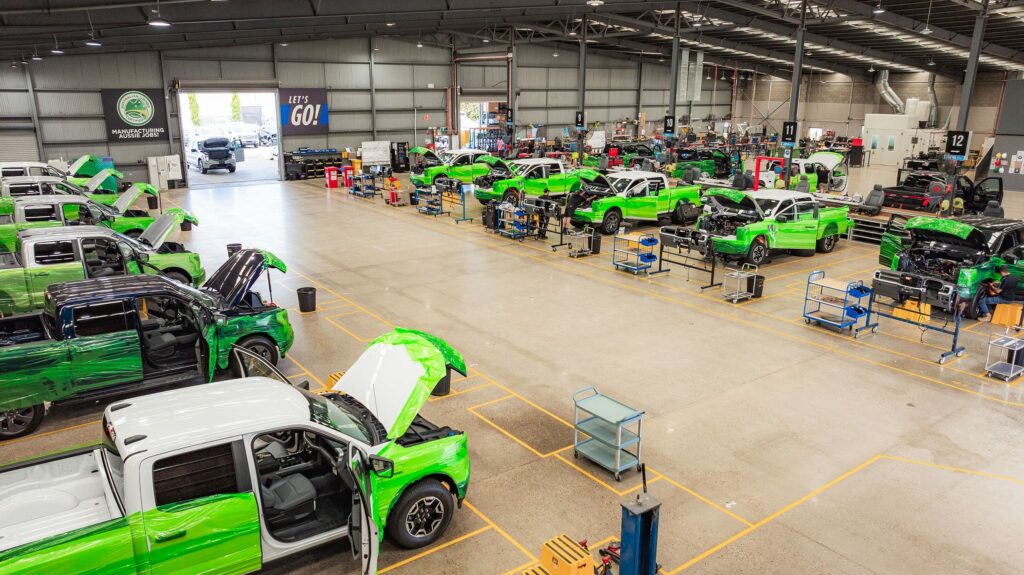
Advanced Manufacturing Queensland (AMQ) is an Australian owned engineering & manufacturing company offering class leading solutions to the automotive and defence industries.
Our facility located in Brisbane, Australia has the capability to take a design concept all the way through to production, providing clients with a comprehensive end-to-end solution.
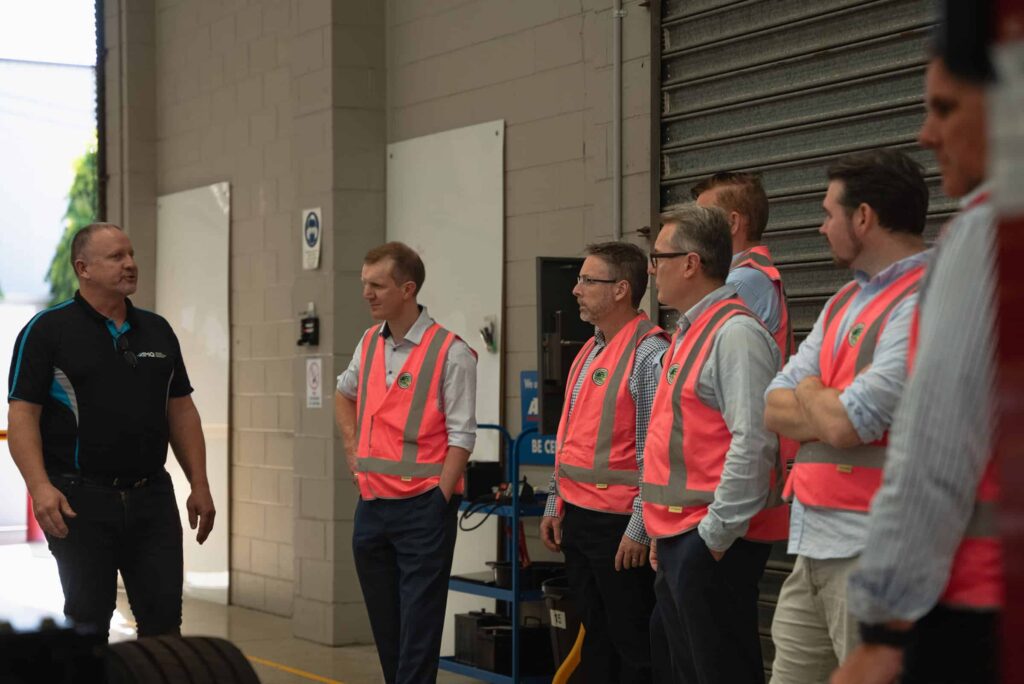
AMQ has partnerships with higher education institutions and is an active member in various committees and groups that are focused on strengthening Australia’s sovereign capabilities and education standards.
At our core is a commitment to customer focus and constant evolution, supported by an engaged team with a passion for advanced manufacturing.
Proudly Australian owned, we are committed to assist other industries onshore their manufacturing.
Australian Owned Certified (AO#8989) business.
LHD to RHD Vehicle Re-engineer & Remanufacture
We have re-engineered and remanufactured thousands of vehicles for both the domestic and international market over the past 12 years.
EV Charging Conversion
Our electrical and software engineers convert CCS1 to CCS2 for Electric Vehicles and validate on both AC & DC Chargers.
Vehicle Upfitting
Design and fitment of site safety packs as well as general accessories and upgrades.
Market Homologation
ADR testing and Rover Compliance.
IP Protections
EV Battery Diagnostics & Repairs
Our team can accurately diagnose and address specific problems within an EV battery pack, such as degraded cells or faulty components, with targeted repairs that will cost a fraction of purchasing a new battery pack.
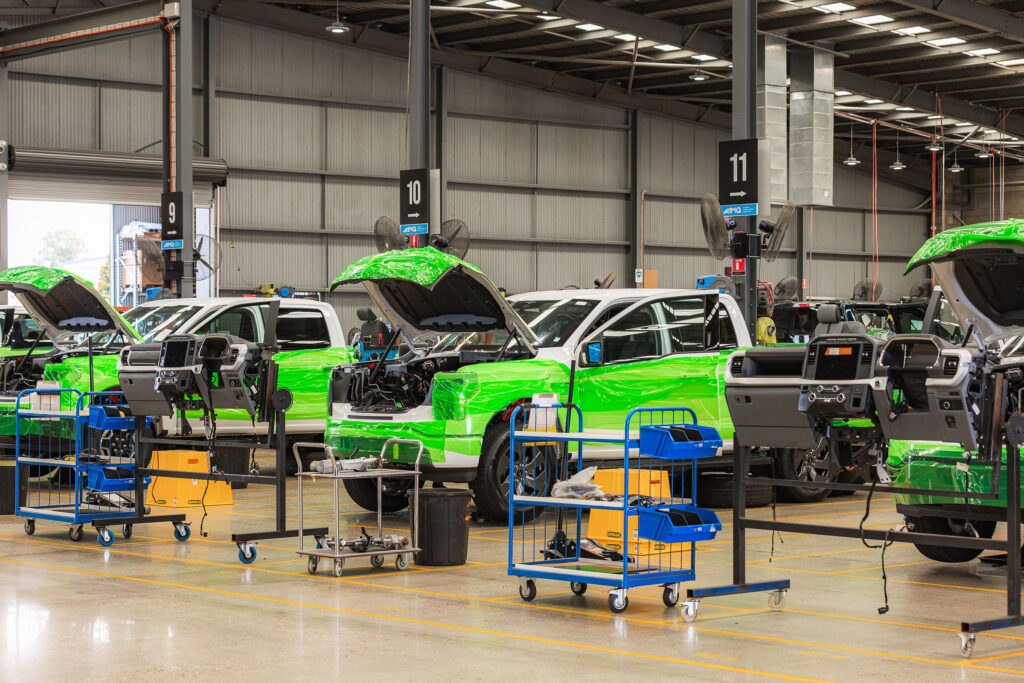
Capability
Engineering & Design
- Mechanical, Electrical & Software Engineering
- Rapid Prototyping (Including 3D Metal Printing)
- Reverse Engineering
- Finite Element Analysis & Durability Testing
- Design For Manufacture
Mechanical, Electrical & Software Engineering

Utilising multi-disciplinary engineering within a company allows collaboration among diverse expertise, leading to holistic and innovative solutions that address complex challenges comprehensively. This integrated approach not only enhances problem-solving capabilities but also promotes efficiency, as teams with varied skill sets work synergistically to deliver well-rounded and optimized products or systems.
Reverse Engineering
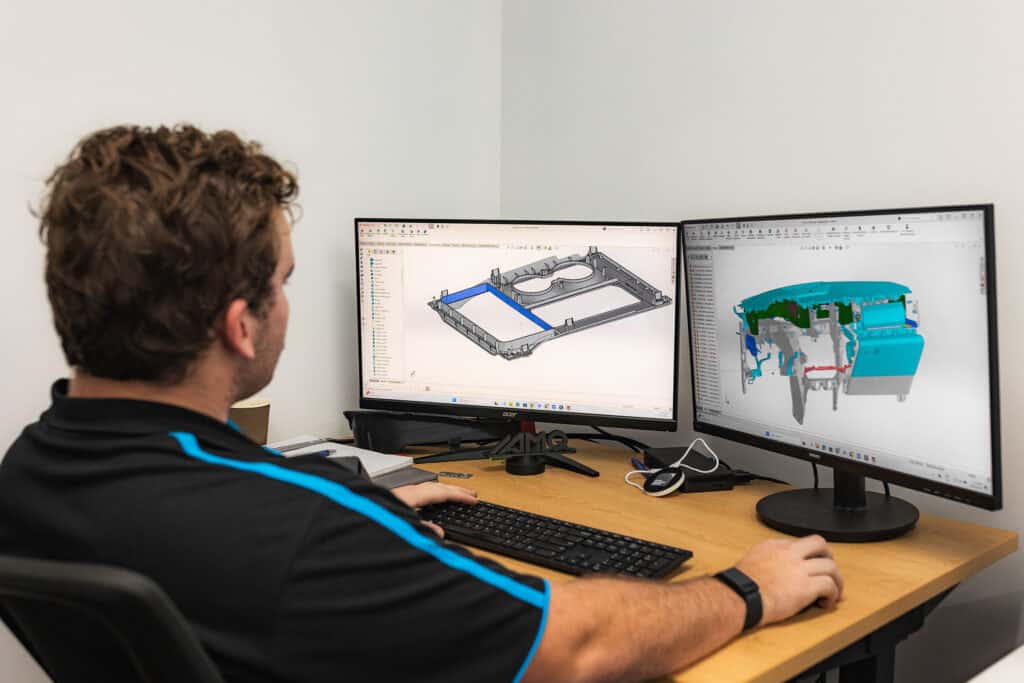
3D scanning is the process of using a device to capture the physical dimensions and characteristics of an object or environment and convert it into a digital model. The resulting digital model can then be used for a variety of purposes, such as designing and prototyping new products, creating virtual reality environments, or even restoring historical artifacts.
Rapid Prototyping
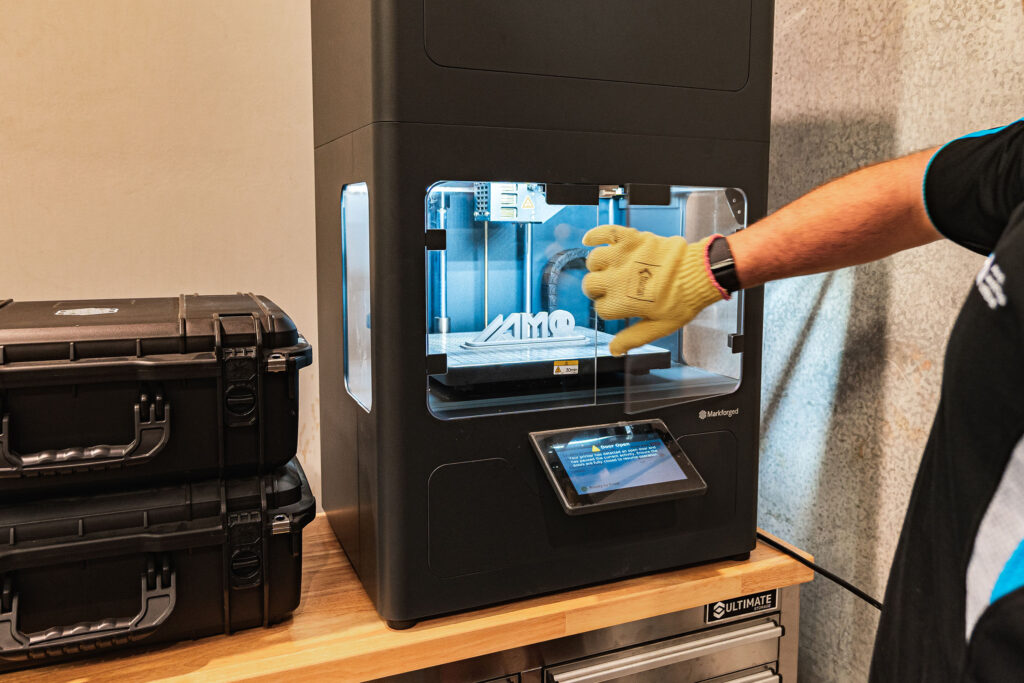
Prototyping is a process of quickly creating a physical model or prototype of a product using 3D printing, CNC machining or other similar technologies.
AMQ’s rapid prototyping services are completed from start to finish in one location allowing our engineers to create functional prototypes in a matter of days or even hours, compared to the traditional manufacturing process, which could take weeks or even months to produce a single prototype. This significantly reduces the time and cost associated with developing a new product.
Finite Element Analysis and Durability Testing
Finite Element Analysis (FEA) is a powerful numerical analysis technique used in engineering and scientific applications to simulate the behaviour of complex systems. It is used to determine the response of a system to a variety of physical stimuli such as heat, pressure, and vibration.
The FEA process involves dividing a complex system into smaller, more manageable pieces known as finite elements. These elements are then subjected to mathematical equations and simulations, which replicate the physical behaviour of the system.
Design For Manufacture
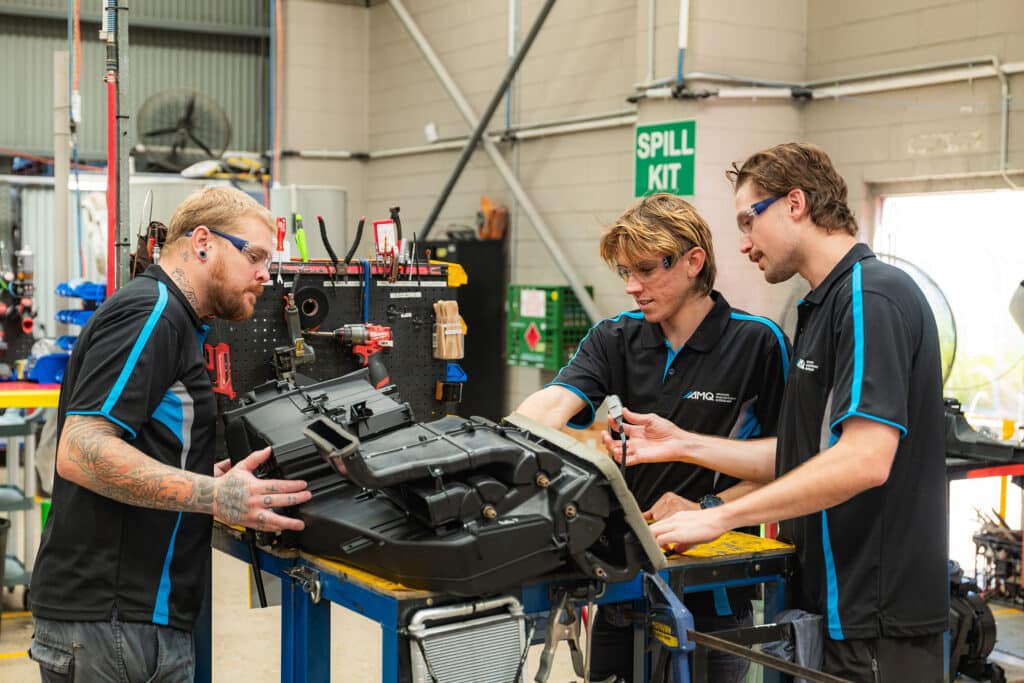
Manufacturing
- Production Process
- Supply Chain Management
- Production Part Approval Process (PPAP)
- Safety
- Additive Manufacturing
Production Process
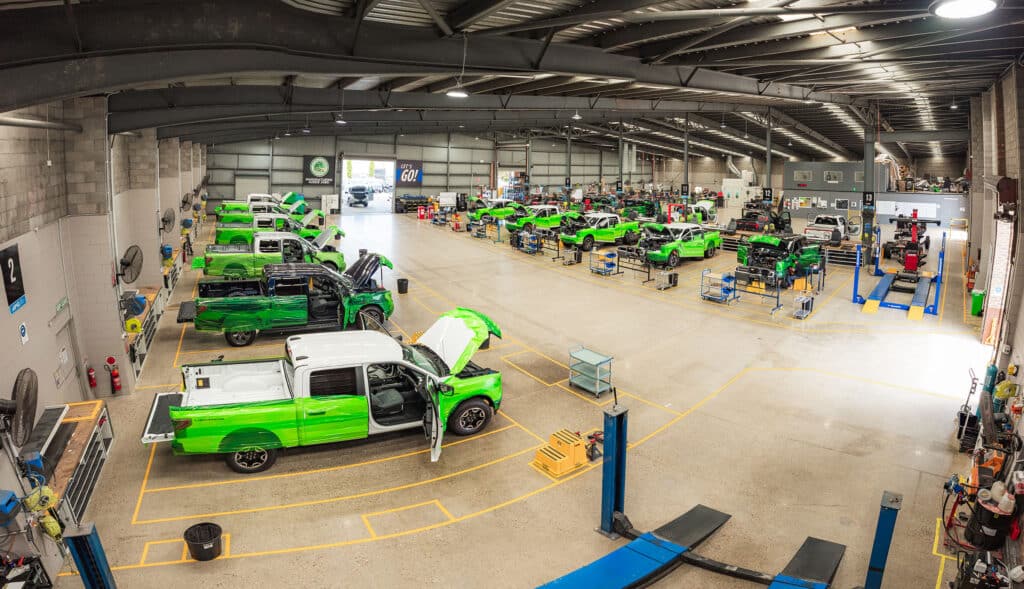
Based on a 8,000 sqm site, AMQ runs full lean manufacturing processes on multiple production lines timed to pulses (Takt time).
Supply Chain Management
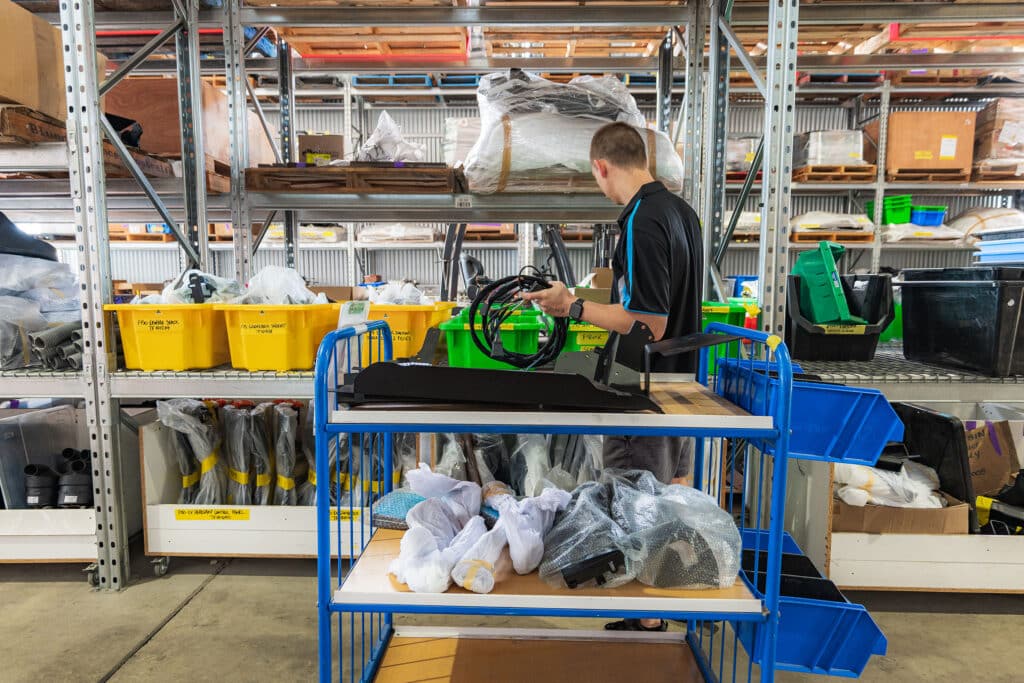
Effective supply chain management in manufacturing optimizes resource utilization, minimizes production delays, and enhances overall operational efficiency, ensuring timely access to materials and reducing costs throughout the production process.
Production Part Approval Process (PPAP)
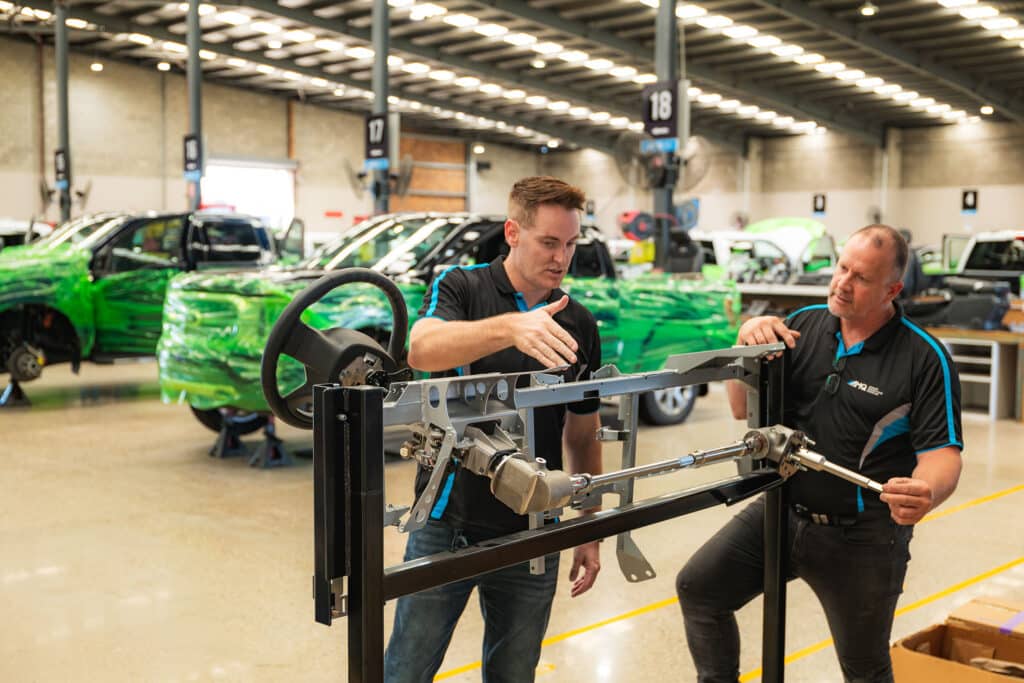
Vetted and audited supply chain with full PPAP on safety-critical components.
Safety
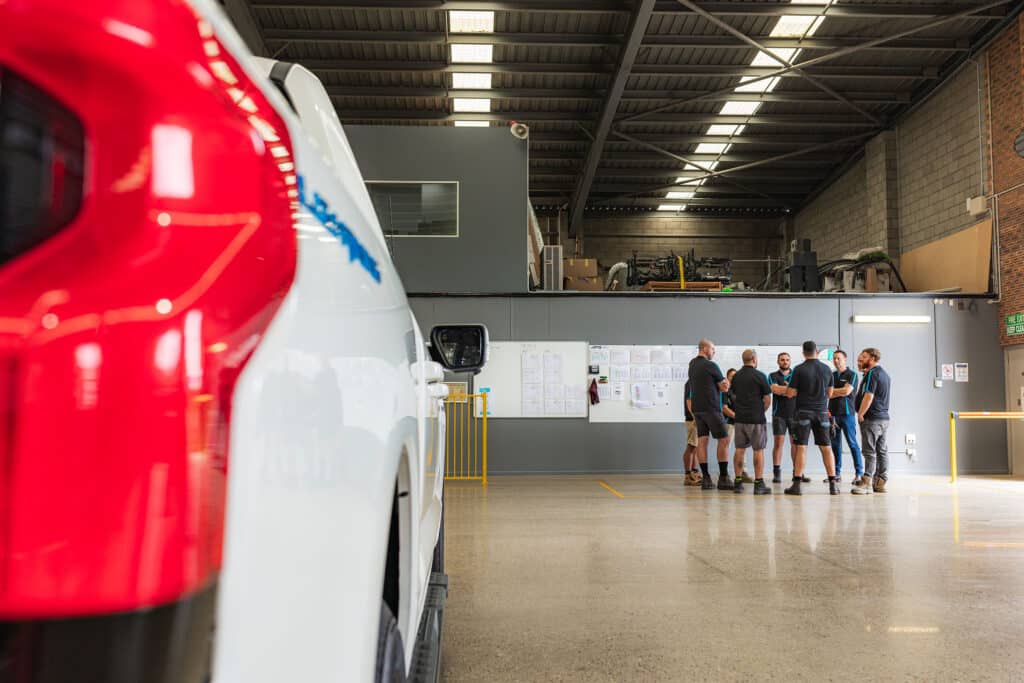
Prioritizing safety in manufacturing not only safeguards workers, preventing accidents and injuries, but also promotes a more secure and compliant working environment, thereby boosting employee morale, productivity, and long-term operational stability.
Additive Manufacturing
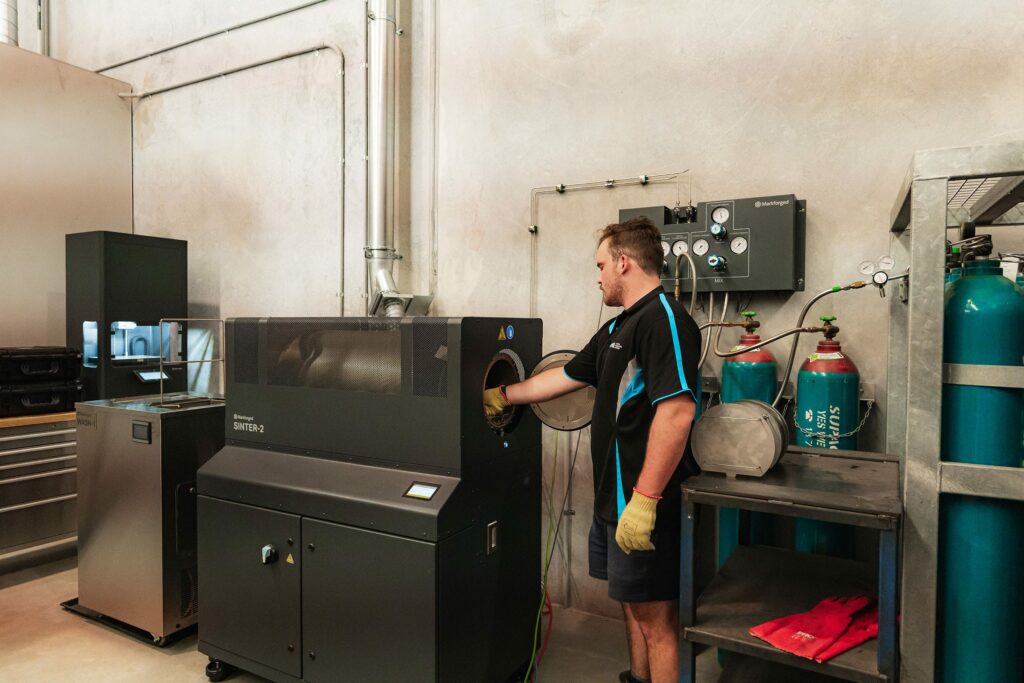
Contact
Our Location
43 Kremzow Road
Brendale, QLD 4500
"*" indicates required fields